オイルシールの主リップ先端温度を測定することで、以下メリットがあります。
1. オイルシールの寿命予測ができる
2. 漏れ原因の究明に役立つ(運転中の主リップ状態変化を推察できる)
3. 最適なゴム材の選定ができる(コスト削減に繋がる)
4. オイルシールに塗布するグリースの選定ができる
5. オイルシール設計にフィードバックができる(無理のない性能向上)
上記を詳しく説明します。
1. オイルシールの寿命予測ができる
各ゴム材には使用最高温度があります。一般的にNBRは100℃、ACMは150℃、FKMは180℃といった具合いです。オイルシールメーカーのカタログには、簡易的な主リップ温度の推定計算式が記載されていますが、シール設計(ゴム材、緊迫力、バレル角度、リップの数など)や運転条件(周速、潤滑、圧力、周辺温度など)によって、主リップ温度は全く異なる結果となるため、精度よく推定することは困難です。例えば、ゴム材が同じNBRの場合であっても、NBRの種類が異なる(NBR1とNBR2)だけで主リップ温度が大きく異なることがあります。これは、ミクロ視点で見た際、NBR1とNBR2で主リップしゅう動面の粗さ(凹凸)の違いや、ゴム材自体の摩擦係数の違いなどが影響しているからです。
以上より、熱電対付きオイルシールを使用して主リップ先端温度を実測することは非常に有効な手段となります。実測した結果、使用最高温度の超過がないことを確認するとともに、主リップ先端温度と使用油種(エンジンオイル/ギヤオイルなど)の組み合わせから、大凡の寿命予測を行うことができます。
さらに精度よく寿命予測をしたい場合には、JISに準拠した浸漬試験(ゴムを高温オイル/グリースに漬けた状態で、引っ張り強さやゴム硬度などの物性値の経時変化を測定)を実施して算出する手法があります。浸漬試験の条件として、「浸漬オイル/グリースの温度=主リップ先端温度」として浸漬試験を行うことで、より実状に近い高精度の寿命予測を行うことができます。
2. 漏れ原因の究明に役立つ(運転中の主リップ状態変化を推察できる)
運転中の主リップ先端温度をモニターすることによって、主リップ状態の変化を推察できます。例えば、安定していた主リップ先端温度が急に上昇したり、乱高下を繰り返すといった場合などです。
温度変化の挙動傾向によっては、「潤滑が切れた」や「緊迫力が低下した」など、主リップ状態変化のモードや、その発生時期を推察することができます(図1)。
それによって、例えば市場でオイルシール漏れ不具合が生じた場合の再現試験において、漏れ原因究明の手助けとなります。
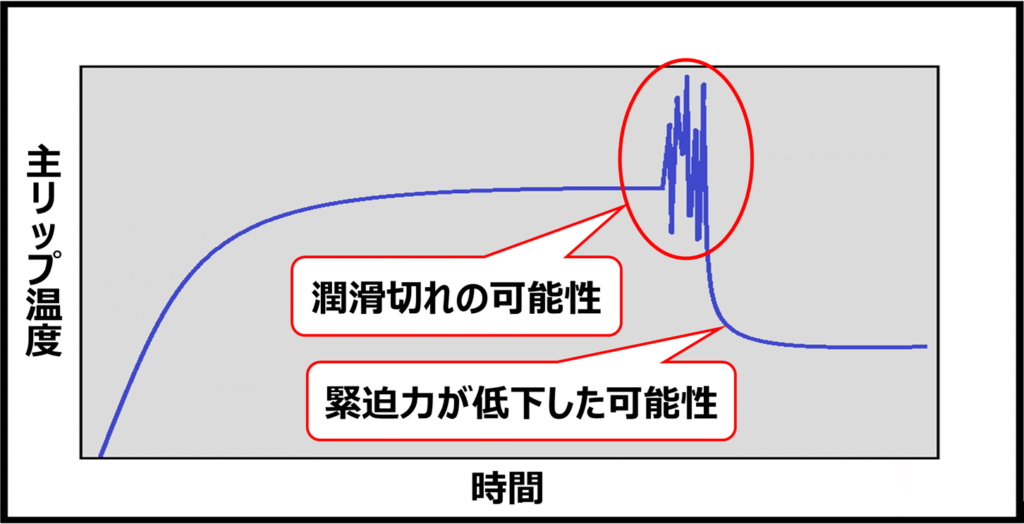
図1
3. 最適なゴム材の選定ができる(コスト削減に繋がる)
例えば、オイルシールのゴム材としてFKMを採用している場合、主リップ先端温度によってはACMやNBRなどで十分にスペックを満足する場合があります。いわゆるオーバースペックの状態です。FKMからACM/NBRなどに切り替えることができれば、スペックを満足しつつコスト削減を行うことができます。オイルシール単価は、FKM→ACMで60%減、FKM→NBRで80%減となることもあります。
4. オイルシールに適した塗布グリースの選定ができる
通常、オイルシールには初期潤滑として主リップ先端周辺にグリースを塗布します。
オイルシールと同様、グリースにも使用最高温度があります。運転時、主リップ先端温度がグリースの使用最高温度を超過した場合、油膜破断による潤滑性の低下が生じることで主リップ摩耗が促進したり、固化したグリースが主リップ周辺に固着することで密封性能が低下するといったリスクがあります。
また、ゴム材とグリースには相性があり、例えば「FKM×ウレア系グリース×高温」の組み合わせは非常に相性が悪く、FKMが早期に硬化することで密封性能を喪失するといったリスクがあります。
上記リスクを回避するために、主リップ先端温度を測定することによってオイルシールに適した塗布グリースの選定をすることができます。
5. オイルシール設計にフィードバックができる(無理のない性能向上)
例えば、主リップ先端温度が想定よりも低かった場合、温度的に無理のない範囲内でロバスト性(=耐偏心/耐振動/耐異物など)向上を検討することができます。耐偏心/耐振動性向上のため主リップのしめしろ/緊迫力をアップしたり、耐異物性向上のためダストリップにしめしろを設けたりなど、無理のない性能向上案を検討し、オイルシール設計にフィードバックすることができます。